Electric furnace transformer
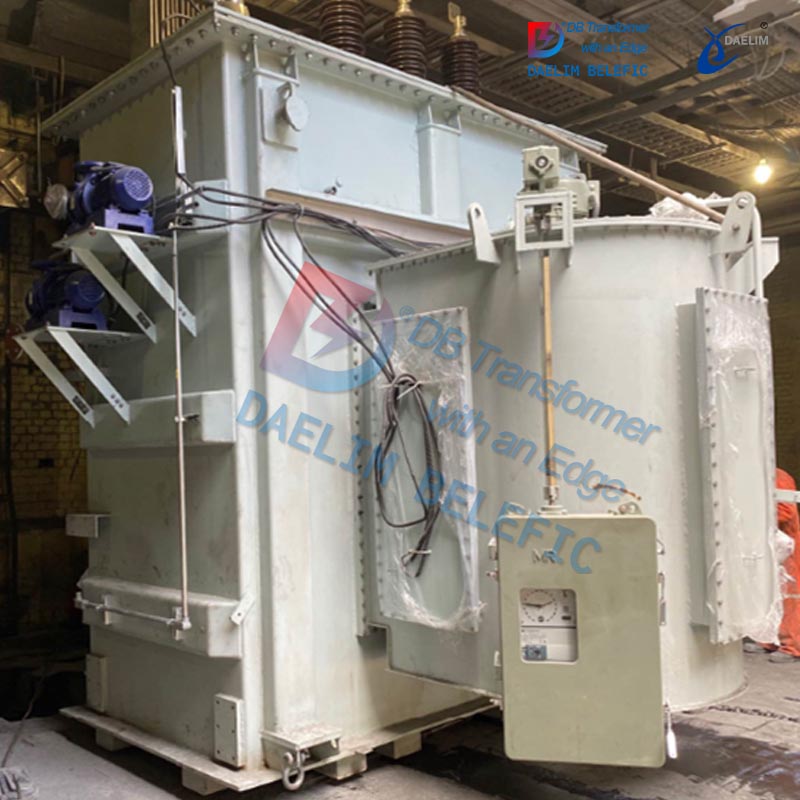
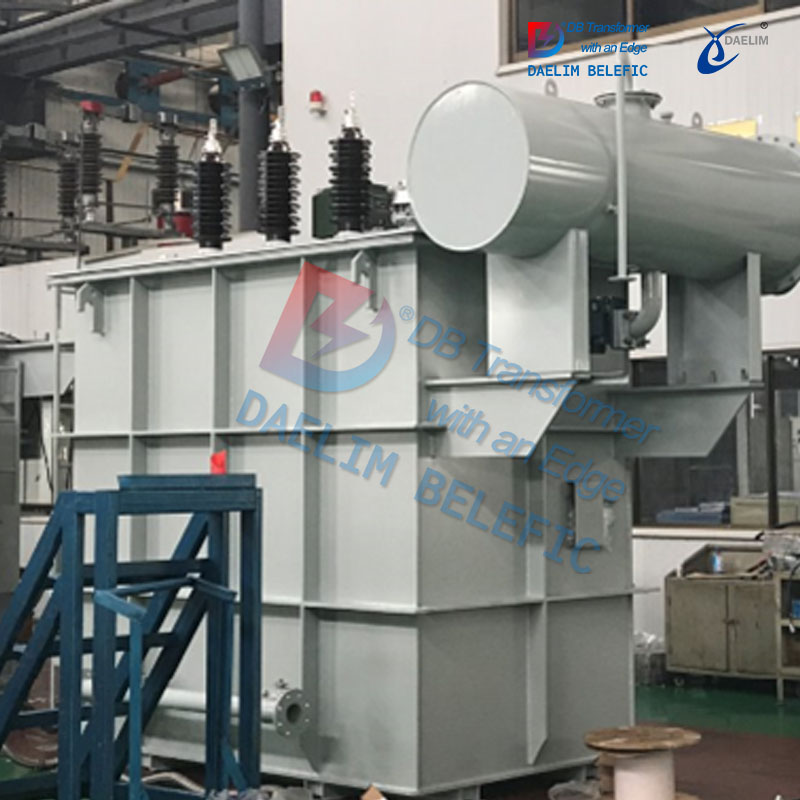
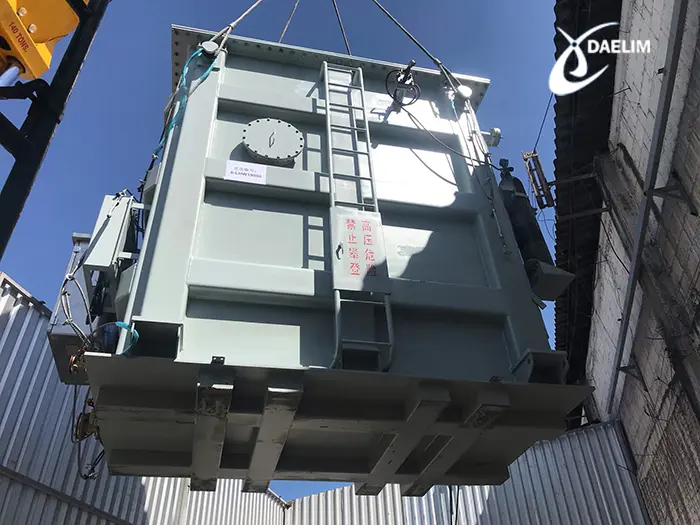
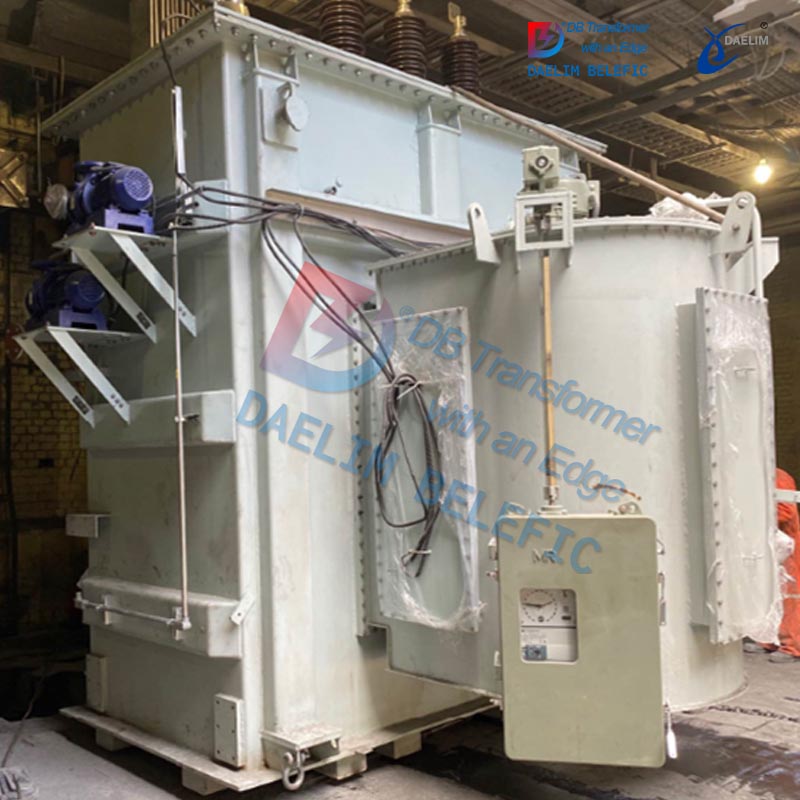
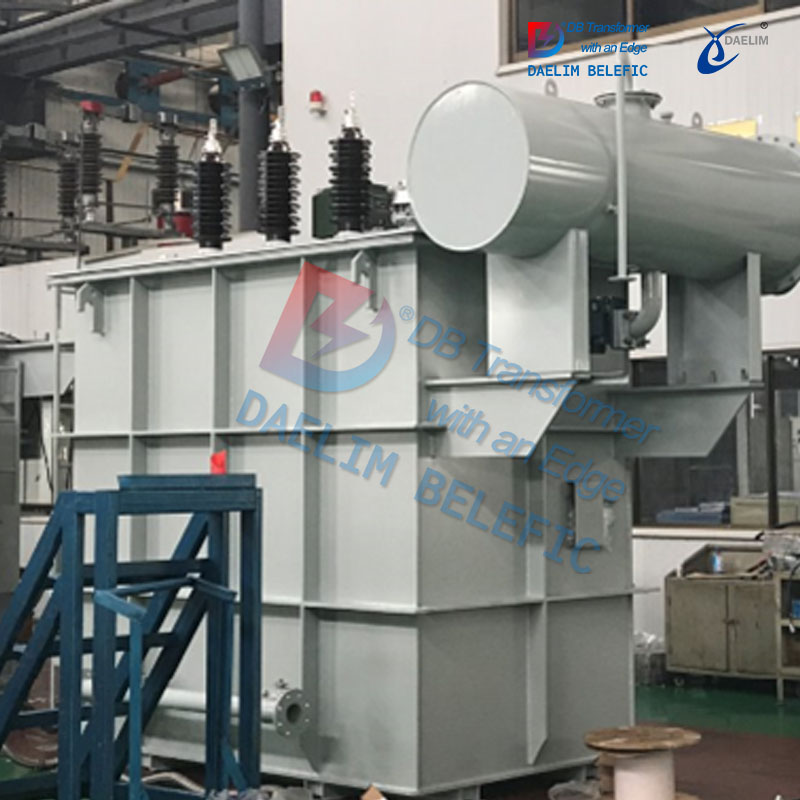
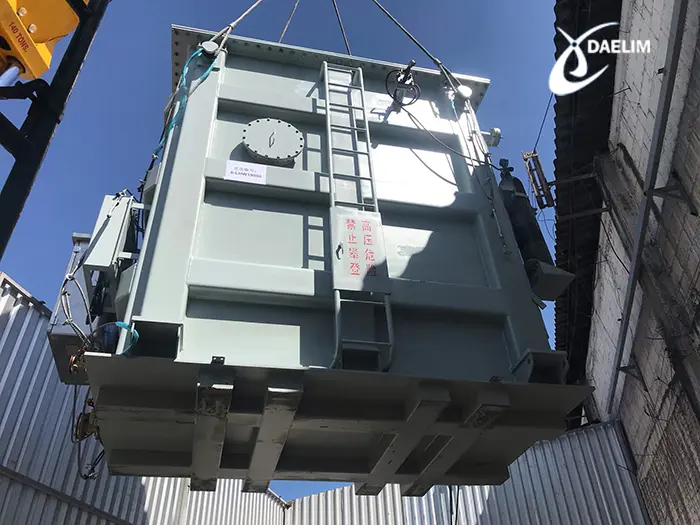
- Primary Voltage Ratings: 20kV
- Secondary Voltage Ratings: 152V & 189.9V
- TYPE: Three phase furnace transformer
- BIL: 150kV
- Standards: IEC IEEE
- Application: Steel Mill
- Power Rating: 6MVA, 20MVA
- Cooling Method: OFWF
The furnace transformer is designed in accordance with IEC/IEEE standards.The image below depicts a drawing of an electric furnace transformer meticulously crafted by Daelim Transformer for a valued Mexican client in 2019. Utilized within their own steelmaking plant, the client acquired two electric furnace transformers, one rated at 6MVA and the other at 20MVA. Following the completion of production, the customer conducted an inspection at our facility. Their satisfaction was evident post-inspection, reaffirming the quality and precision of our work.
Quote Now
Two electric furnace transformers were delivered by Daelim Transformer to a longstanding steel company in Mexico with a century-old history in July 2019, replacing outdated units. These new transformers operate at high voltages and manage significant electrical loads. Constructed from robust structural and insulation materials, they withstand high temperatures, vibrations, and electrical interference, proving ideal for the challenging environments of steel plants.
Key Features
- High tolerance to electrical, thermal, and mechanical stresses
- Wide voltage range and high current handling capacity
- Resilient to frequent short circuits on the secondary side
- Compact and cost-effective
- Service life exceeding 30 years
Supervision and protection
Winding thermometer (alarm and disconnect).
Gas relay - Buchholz with 2 contacts (alarm and trip).
Oil thermometer with 2 contacts.
Magnetic oil level indicator with 1 contact.
Furnace Transformer Scope
- High voltage capability up to 110kV
- Power rating up to 300MVA
- Cooling methods: ONAN, ONAF, OFWF
Cooling Options
- Oil-water heat exchanger for forced oil cooling: ensures large capacity and operates at low oil temperatures, maintaining prolonged service life even under overload conditions.
- Water cooling: suitable for constrained spaces
With extensive expertise in designing and manufacturing electric furnace transformers, Daelim Transformer guarantees alignment with industrial requirements for specific harmonics and high currents. Contact us now for customized plans and quotations.
Furnace Transformer Drawing
Electric furnace transformers that have been completed
Electric furnace transformer installation site
Design options:
− Direct or indirect regulation
− On-load tap changer
− Built-in reactor for long-arc stability
− Secondary bushing arrangements and designs, air or water-cooled
− Internal secondary phase closure (internal delta)
− RC-SA high voltage protection system
Electric Furnace Transformer Type
An electric furnace transformer is a transformer specially designed to provide power for various electric furnaces. Industrial electric furnace transformers can be roughly divided into three categories: Resistance furnace transformers, Electric arc furnace transformers, and Induction furnace transformers.
Learn more about Electric Furnace Transformer
Resistance furnace transformers are used in resistance furnaces and salt bath furnaces for mechanical parts heating, heat treatment, powder metallurgy sintering, non-ferrous metal smelting, etc. Since the resistance of the heating element is too small, or the resistance of the heating element is too large during the heating process, a resistance transformer needs to be equipped between the furnace and the power grid to reduce and adjust the input voltage of the electric furnace.
Resistance furnace transformer
Resistance furnaces and salt bath furnaces for heating of mechanical parts, heat treatment, powder metallurgy sintering, metal smelting of non-ferrous electric furnaces and transformers, etc. Because the resistance of the heating element is too small, or the resistance of the heating element changes too much during the heating process, a resistance furnace transformer needs to be equipped between the furnace and the power grid to reduce and adjust the input voltage of the electric furnace. Small-capacity, low-voltage resistance furnace transformers, and salt-bath furnace transformers are mostly dry-type transformers with box shells and natural cooling; resistance furnace transformers with medium capacity (hundreds to thousands of VA) are mostly oil-immersed self-cooling transformers; Large capacity is forced oil circulation water-cooled transformer.
Electric arc furnace transformer
Special transformers for powering electric arc furnaces are used in iron and steel smelting. It has a large capacity, complex structure, and high technical requirements. The secondary side voltage is low, generally from tens of volts to hundreds of volts, and it is required to be regulated within a large range; the secondary side current often reaches thousands to tens of thousands of amps.
In addition, in iron and steel smelting, the melting period requires high power, and the transformer is required to have a 20% overload capacity within 2 hours. In the steelmaking process, since the collapse of the charge is likely to cause a short circuit of the electrodes, the primary side of the electric arc furnace transformer should be connected with a current limiting reactor, or it should have a larger impedance of the electric furnace transformer to limit the short-circuit current. The operation of the electric furnace also requires the power supply transformer to be able to adjust the voltage. There are two ways to adjust the voltage of the electric furnace transformer.
①Direct voltage regulation method: On the primary winding of the transformer, the lead-out tap is connected to the tap changer. △-The y switchover can also be used between the three phases of the primary side to realize the voltage regulation of the secondary side. △-Y switching is a very economical way of voltage regulation, which can reduce the secondary voltage to 1/ of the original without changing the number of turns on the primary side. Because each phase winding has 9 taps, plus △-Y switching, a total of 2 × 9 or 18 levels of voltage can be obtained.
②Indirect voltage regulation method: The indirect voltage regulation method with series transformer is shown in the figure. Main transformer 1 is a three-winding transformer (see multi-winding transformer), winding 1 is a high-voltage winding, which is connected to the power grid; winding 2 is a winding with a tap, which is connected in series with the primary winding 4 of series transformer II through a tap changer; winding 3 It is connected in series with the secondary winding 5 of the series transformer II to supply power to the electric furnace load. By changing the primary voltage of series transformer II through the tap changer, the output voltage of windings 3 and 5 can be changed. The 3 and 5 windings connected to the load generally have only 1 to 2 turns and are usually made of a figure-8 coil of copper or aluminum plate.
Sense furnace transformer
The induction furnace for melting ferrous and non-ferrous metals is essentially a special electric furnace transformer. There are two types of induction furnaces: iron core and ironless. An iron core induction furnace is a transformer with an iron core and a short-circuit secondary winding. The primary winding of the transformer is connected to the power supply, and the secondary winding actually has only one turn, which is the molten metal installed in the melting tank. When the primary winding has a current, the secondary winding will generate an induced current, which flows in the slot, thereby generating heat and melting the metal.
Structural features
The iron core of the electric furnace transformer is made of a high-quality oriented silicon steel sheet, which is processed by an automatic cutting line, 45-degree full miter seam, no punching, and no weft glass adhesive tape binding process. The coil adopts the latest international main longitudinal insulation structure, and the structure and insulation of the winding are reasonably selected to ensure that the winding has sufficient mechanical strength.
It has the characteristics of strong short-circuit ability, strong overload ability, high efficiency, low loss, safety, and reliability. The working principle of the electric furnace transformer, the electric furnace transformer is the power transformer of the steelmaking electric arc furnace, and the capacity of the electric furnace transformer is configured according to the size of the electric arc furnace and the smelting process.
It meets the requirements of the smelting process by means of pressure regulation. There are two types of voltage regulation: on-load voltage regulation and non-excitation voltage regulation. Large-scale electric furnace transformers with on-load voltage regulation do not have series reactors, and small and medium-sized electric furnace transformers without excitation voltage regulation can be divided into two types series reactors and those without reactors. Change the impedance at two voltages. The former relies on the input and removal of the series reactor to change the impedance. The latter changes the winding impedance by changing the connection method of the high-voltage windings of the furnace transformer itself.
Related Products
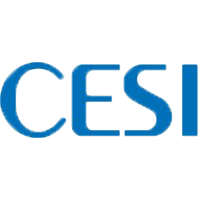
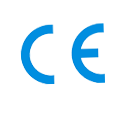
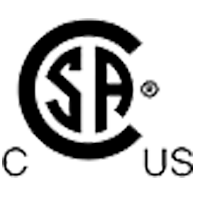

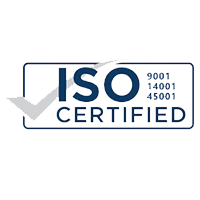
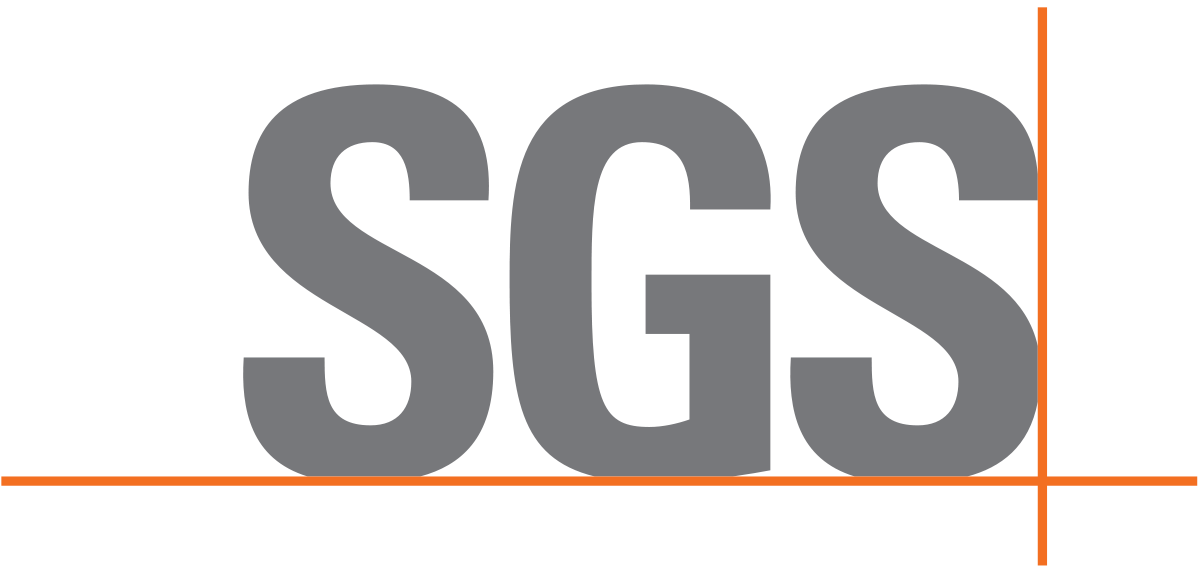
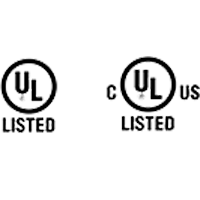
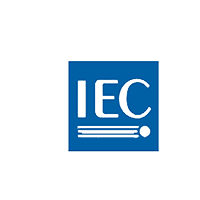
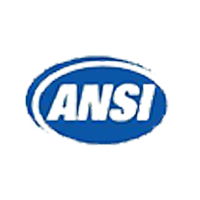