Dry Type Transformer Cooling Methods
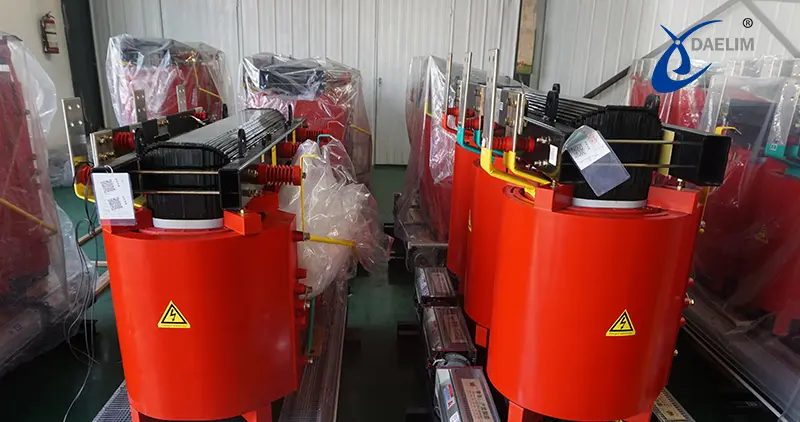
This article is all about understanding the dry type transformer cooling methods that you can install for effective and efficient cooling of your dry type transformers.
We will discuss different types of cooling methods, how the cooling method works, what different parts are there in any cooling system, and what advantages and disadvantages that are associated with each dry type transformer cooling method.
Contact Daelim TransformerDifferent Dry Type Transformer Cooling Methods
Technically speaking, you can only observe three different types of dry type transformer cooling methods. Out of those three different transformer cooling methods, two methods are very common and are very widely used in the transformer industry while the third one is not that common and you will hardly see it in commonly used transformers that are installed in neighborhoods.
Natural Air Cooling (AN)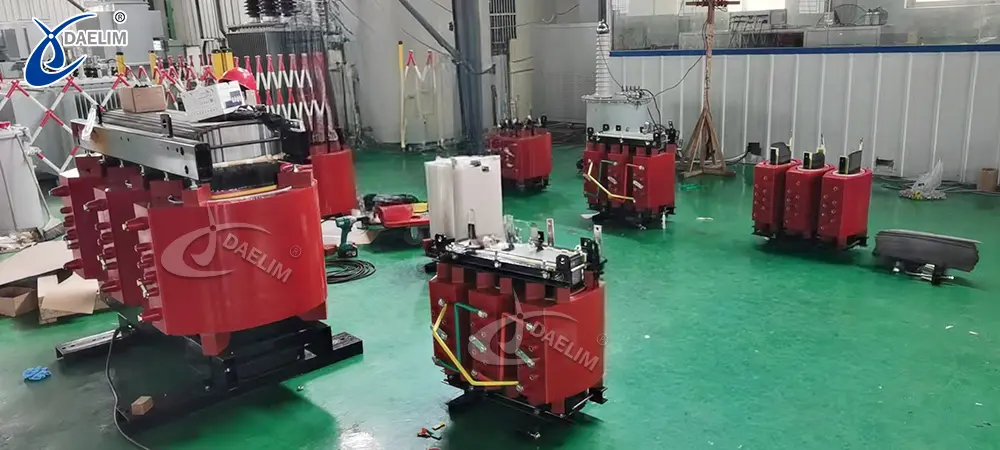
The first method that we will discuss today is an air natural cooling transformer method for dry type Transformers. From all the different types of cooling methods that you can see in a dry type Transformer the air natural cooling method is the most widely used Transformer cooling method.
What is Natural Air Cooling for a Dry Type Transformer?
The air natural cooling transformer method relies on the natural flow of air over the Transformer winding. The natural flow of air over the heated Transformer winding will absorb the heat of Transformer winding using the process of natural convection.
Reading more about Dry Type Transformer
What Transformer Parts are Involved in Natural Air Cooling?
There is absolutely no additional special part needed for the natural air cooling method of your dry drive transformer. As your dry type transformer winding is covered in resin and it can be exposed to the outer atmosphere. So the winding of your Transformer will be exposed to the fresh outer air and there will be no need of any type of special covering or design feature that allow the flow of the he did Transformer winding.
Working Principle of Natural Air Cooling for a Dry Type Transformer?
Air natural cooling transformer method of your dry type transformer depends on the working principle of free convection mode of heat transfer. In free Convection mode of heat transfer, the heat from your Transformer winding will first be transferred to the resin covering the winding. Then the heated reason of your Transformer will transfer the heat to the air surrounding it.
The surrounding air when once absorbed the waste heat will be naturally less dense, then it will naturally flow upward, away from the transformer and the fresh air will move to word the Transformer winding. This process continues till there is waste heat being produced by the Transformer winding.
Advantages of Natural Air Cooling
- The air natural cooling transformer method is the simplest method possible with no maintenance and no cost associated with it.
- This also makes the natural air cooling method the most environment friendly, the most quiet and Ensures the most compact design possible for a dry type transformer.
Disadvantages of Natural Air Cooling
- The biggest advantage of the natural air cooling method also became its biggest limitation, as this method limits the cooling capacity, transformer size and its power rating.
- The method is also the least efficient cooling method and offer very low resistance against any overloading condition
- This cooling method also offers limitations and restrictions about the Transformer installation and space requirement, specially in Indore installations.
Forced Air Cooling (AF)
The second Transformer cooling method that we will discuss here is force air cooling method as it is this the second most widely used cooling method in dry type Transformers.
What is Forced Air Cooling Method
The forced air cooling method of your dryer type transformer involves cooling of your Transformer winding using fresh air that is being forced to flow over the heated Transformer winding. The air when forced on to the Transformer winding absorbs and removes its waste heat and thus completes the Transformer cooling task.
Transformer Parts Involved in Forced Air Cooling Method
The forced air cooling method needs a cooling fan that can force air on to the heated Transformer winding. And to sport the cooling fan it Transformer will need a complete housing on which the calling fan can be installed secularly.
Other than this Transformer will need a complete electrical setup that can provide the cooling fan the required voltage and the current for safe and reliable operation. Depending upon the application and the side of installation the Transformer might also need a structure to protect the cooling fan from Harsh environmental factors like rains.
You may enjoy: Step-by-Step Guideline On Installing A Transformer
Working Principle of Forced Air Cooling Method
The working principle of the forced air cooling method of your dry type electrical transformerIs based on the working of forced Convection heat transfer method. Heat produced at your Transformer winding is first transferred to the resin.
When the temperature of the transformer winding has reached the point where natural Convection cannot cool the winding any further the Transformer cooling fan starts and forces more air to pass over the Transformer winding and remove the based heat using force Convection method.
As more and more fresh air with low temperature is available at the Transformer winding the rate of heat transfer from the Transformer winding to the fresh air is much higher as compared to the natural convection.
Advantages of Forced Air Cooling Method
- The forced air cooling method has a much greater rate of cooling and also offers variable rate of cooling providing effective protection to the Transformer winding in case of overloading when there will be extra heat generated by the Transformer winding.
- The forced air cooling methods allow you to select a Transformer of different sizes and high power capacity as compared to the Transformer using only natural air cooling methods.
- Air cooling method is also considered good for harsh environments where the surrounding atmospheric temperature is usually higher especially during summer season.
Disadvantages of Forced Air Cooling Method
- A forced air cooling method involves a cooling fan, its mounting and all the associated electronics so there will be a higher initial cost of the transformer.
- The fan, its mountain and associated electrical system need continuous maintenance to keep up the efficiency and effective operation.
- There is usually a considerable level of noise generated by the Transformer cooling fan and there is also a continuous and regular maintenance required by the fan and its associated parts.
Learn more: Cast Resin Transformer
Coolant based Dry Type Transformers Cooling Method
The third cooling method is quite unique and it's not quite commonly used in small and regular dry type Transformers. It is used in special and dedicated dry type transformers whose application performance and reliability is white sensitive based upon its application.
What is Coolant based Dry Type Transformers Cooling
The coolant based dry type transformer cooling method relies on a liquid that works as a coolant to remove the waste heat from the dry type transformer. Now the coolant doesn't directly come in contact with either the resin or the Transformer winding but it indirectly removes the waste from the Transformer winding using a heat exchanger. The coolant can be a refrigerant or any chemical that can easily absorb heat from the Transformer winding and efficiently transfer it to the external environment.
Parts Involved in Coolant based Dry Type Transformers Cooling
Is usually a complete heat exchanger involved in this coolant based dry Transformer cooling method. The heat exchanger is usually designed in a manner that the tube for the coil of the heat exchanger is in direct contact with the Transformer winding for the resin covering the Transformer of winding.
Exchanger can be of any design but in most cases the heat exchanger consists of a single tube. The tube usually makes a spiral around the Transformer winding in a manner that it is in constant and direct contact with the resin that covers the Transformer winding in dry type transformer.
Other than that, there will be a tank attached to the heat exchanger that will contain the coolant and there will be a pump that will force the coolant to circulate through the entire length of the heat exchange tube. It also depends upon the design of the heat exchange but there will be a mechanism available to remove the heat from the coolant as well.
There can be a separate cooling fan base cooling mechanism that can force fresh air over the tube containing the heated coolant. This can remove the waste heat from the coolant and transfer it to the surrounding atmosphere.
The heat exchanger also needs the supporting structure and the electrical connection to power the electrical pump and cooling fan. There can also be infrastructure in place to protect the heater changes from Harsh environmental conditions.
Working Principle of Coolant based Dry Type Transformers Cooling
The working principle of the coolant based dry type Transformer cooling method is based on the principles of conduction and convection method of heat transfer. Heat generated at the Transformer winding is first transferred to the resin covering the Transformer winding. From there the heat will be transferred to the tube of the heat exchange method of heat transfer.
From there the heat from the tube will be transferred to the coolant that moves inside the tubes of the heat exchanger using the principle of convection based cooling method. When it moves forward, it absorbs all the heat of the winding and moves to the region where the cooling fan will remove heat from the heat exchanger coolant.
The principle of conduction and convection method of heat transfer will be used again but in Reverse mechanism to transfer the heat from the coolant to the fresh air passing over the tube of the heat exchanger.
Advantages of Coolant based Dry Type Transformers Cooling
- This coolant based dry type transformer cooling method over the best heat transfer rate and can be used in all type of sensitive installations where reliability and efficiency is the main concern
- This method offers the best result in case of overloading and and especially in areas where ventilation is not that good for natural air or force air bass cooling methods.
- Desh calling methods of versatility in terms of transformer size, power capacity, and application.
Disadvantages of Coolant based Dry Type Transformers Cooling
- This cooling method needs a complete dedicated mechanism of cooling that increases the cost of the transformer.
- The dedicated cooling mechanism needs dedicated maintenance and replacements of parts during scheduled maintenance. This also increases the cost of the overall project.
- This cooling method also has a high operational cost and also the coolant used in the changer Raises the environment concerns in case of any leakage.
Comparison of Cooling Methods
Cooling Method | Efficiency | Cost | Maintenance | Application Suitability |
Natural Air Cooling (AN) | Least efficient due to limited heat dissipation | Lowest cost, no additional components required | No maintenance required | Suitable for small transformers with low power ratings and well-ventilated areas |
Forced Air Cooling (AF) | More efficient than natural air cooling, provides better heat dissipation | Higher initial cost due to cooling fan, housing, and electrical setup | Requires regular maintenance for the fan and electrical components | Suitable for larger transformers, high-power applications, and harsh environments |
Coolant-Based Cooling | Most efficient with high heat dissipation and reliable cooling | Highest cost due to heat exchanger, coolant, pump, and cooling fan | High maintenance due to coolant circulation, heat exchanger, and potential environmental concerns | Suitable for sensitive applications requiring high reliability and efficiency, especially in low-ventilation areas |
Conclusion
We have discussed three different dry type transformer cooling methods and each method of advantages and disadvantages of its own. The air natural cooling transformer method is the simplest as it does not need any parts or maintenance and has zero operational cost. The forced air transformer cooling method offers greater cooling rate and good protection in case of overloading. The coolant based methods are highly efficient but have high initial and operational cost limits in applications.
Follow Up
Dry type transformers are very widely used in small to medium load capacity applications and need cooling methods to deliver reliable and safe electricity. We at Daelim Transformer offer dry type transformers of all types, sizes, and power ratings. We also deliver dry type transformers wil custom cooling systems for sensitive applications.
If you have any questions about dry type transformers or about their cooling method. You can contact us and we will answer all your questions.
Related Products
Related Article
VPI Transformer
VPI transformers are high-performance, environmentally friendly, and low-maintenance transformers, ideal for industries requiring reliable power distribution. They feature vacuum-pressure impregnated windings for superior insulation, thermal endurance, and extended lifespan. VPI transformers offer reduced noise, improved efficiency, and are available in multiple power ratings, making them suitable for manufacturing, renewable energy, critical infrastructure, and marine applications.
Cast Resin Transformer: Definition, Types, Benefits, Applications, Maintenance
The cast resin transformer is a type of dry transformer that uses epoxy resin to encapsulate the windings and core, providing excellent insulation and environmental protection.
Addressing the Iberian Blackout: A Wake Up Call
A major blackout in Spain and Portugal exposed critical grid vulnerabilities, especially with renewable integration, transformer infrastructure, and reactive power control. Daelim offers fast-delivery, high-quality, custom transformers—ideal for modernizing outdated systems and supporting renewable energy projects. Contact Daelim for reliable, future-ready transformer solutions.
Distributed Energy and Temporary Power
Daelim Transformer provides reliable, efficient solutions for the growing demands of distributed energy and temporary power systems, including solar, wind, and data center applications. With deep expertise and proven performance, Daelim ensures safe and sustainable electricity delivery while addressing the unique challenges of today’s evolving energy landscape.
The Impact of Operating Environment on Transformer Design
Electrical transformers are custom-designed based on specific application needs, not a one-size-fits-all model. While voltage input/output is important, other operating conditions also impact design. This article explores how environments like renewable energy plants and data centers influence transformer design, highlighting the importance of tailored solutions for efficient electricity distribution.