Comparing Amorphous Core and Silicon Steel Core Transformers
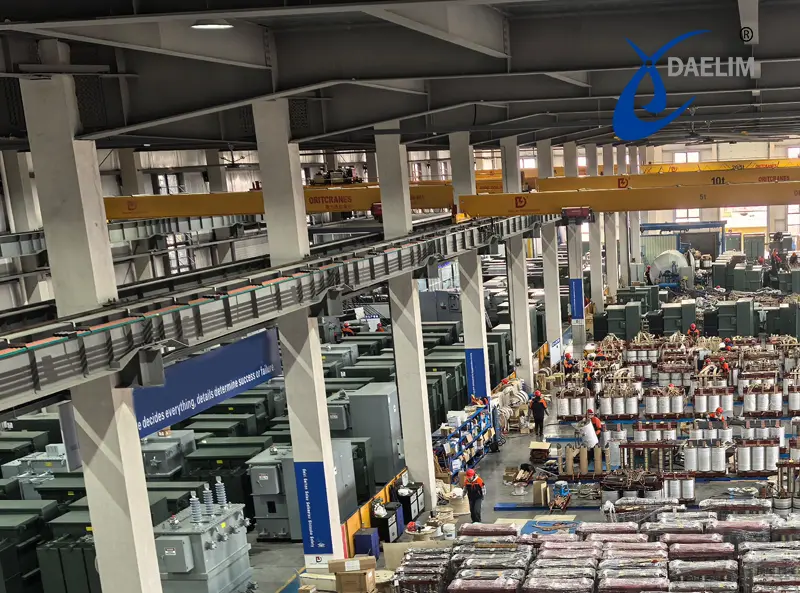
Electrical transformers are an important part of our electricity distribution system that heavily rely on the transformer core for delivering electricity efficiently. The electric transformer core looks like a very simple metallic part of the transformer but plays a crucial role of transferring power from primary wind to secondary winding efficiently.
The transformer core solely relies on its material to transfer electrical power efficiently and two of the most widely used materials are amorphous and silicon steel. To better understand amorphous core and silicon steel core transformers, we will have a brief comparison of both materials. We will compare their design, construction, manufacturing, working, and applications.
Contact Daelim TransformerMaterial Comparison of Amorphous and Silicon Steel Cores
The amorphous core transformer has their name applied and an amorphous metal alloy in their transformer core as silicon steel transformer core uses a specific type of silicon steel for their core manufacturing. Each material has its own unique properties for which it can be used for the construction of the transformer core and we will discuss each and every property here in detail.
Learn more about Amorphous Transformers
Atomic or Grain Structure
The amorphous metal alloys are non crystalline in their atomic structure and their grain structure is like glass atomic structure. As the atoms of amorphous metals are always arranged randomly so there is no long range order in its atomic structure. This is one of the main reasons why this transformer core material is used is that its structure minimizes magnetic domain pinning in the electrical transformer that allows much smoother magnetization of the transformer core and reduces the core losses.
Very opposite to this, the silicon steel has a very particular crystalline structure as its main grain or atomic structure. This specific orientation of grain is due to the cold rolling and annealing of the material during the manufacturing stage. The crystalline grain structure of the silicon steel allows the magnetic flux flow in one direction thus improving the efficiency of the transformer core. The crystalline structure however offers more resistance to the magnetic domain movement as compared to that of the amorphous metal.
Electrical Resistance
The amorphous metal alloys typically offer high electrical resistivity which is around 130 to 150 micro ohm centimetre whereas the silicon steel lamination sheets that are used in the transformer core material have moderate electrical resistivity that ranges from 45 to 50 micro ohm centimetre. The high electrical resistivity of the amorphous metal helps reduce eddy current losses and this improves overall efficiency at specifically high frequency applications. Silicon steel's lower electrical resistance allows more eddy current formation in the transformer core material especially at high frequencies.
Magnetic Coercivity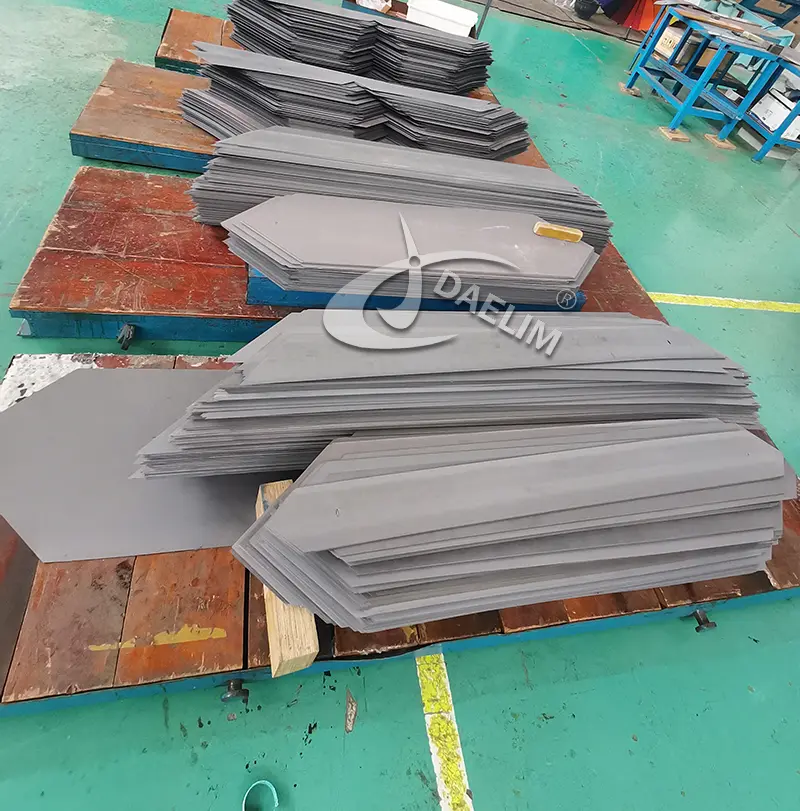
The magnetic coercivity is an indication of how easy it is for a metal to magnetize and demagnetize. The amorphous metal alloy has a low magnetic coercivity which means it takes very little energy to magnetize and demagnetize the amorphous metal core. This makes an amorphous metal alloy core ideal for soft magnetic applications. The silicon steel transformer core material has a moderate level of magnetic coercivity due to their crystalline structure. In crystalline structure the domain wall motion is somewhat distinct when we compare it to that of the amorphous metal.
Magnetic Permeability
The amorphous core material offers excellent magnetic permeability at high frequencies. The soft magnetic nature of this material allows rapid switching in the electrical transformer core and thus reducing core losses in the electrical transformer. The silicon steel also has high magnetic permeability but it is not as high as that of the amorphous metal alloy at high frequencies. The silicon steel transformer core is suitable for 50 or 60 Hz application as their performance starts to decrease at higher frequency due to high eddy current and hysteresis losses.
Magnetic Flux Density
The amorphous metal alloy has moderate magnetic flux density but it is much lower than that of the silicon steel as the silicon steel has quite high magnetic flux density reaching up to 2 Tesla. The higher magnetic flux intensity of the silicon steel allows it to handle much higher magnetic loads making it ideal for large power transformers whereas the amorphous metal alloys are recommended for medium size transformers for sensitive application.
Comparison of Construction of Each Core
The amorphous core material of the transformer is made from iron based alloy that contains elements like boron and silicon whereas the silicon steel itself is made from the molten alloy that is rapidly cooled at extremely high rate this gives it the crystalline structure.
You may enjoy: Construction of Three Phase Transformers
Amorphous Core Construction
Once the amorphous metal is created in the furnace it is solidified into ribbon like sheets using the method called a planar flow casting method. In this method the molten material is ejected onto a rapidly rotating water cooled wheel that rotates and cools the molten metal into thin ribbon like sheets. The thickness of the sheet is extremely small with only 20 or 30 micrometer thickness. These extremely thin sheets help minimize the eddy current losses in the material and in the transformer core.
To get the exact shape of the required transformer core the amorphous metal ribbon like sheets are then cut into the specific length and shape. The extremely thin sheets that are cut into the required shape and length are then stacked together layer by layer to form a thick transformer magnetic core. Depending on the requirement the shape can be rectangular, C shape or toroidal.
After getting the required shape and size of the transformer core the final assembly of the transformer core is processed through the heat treatment process called annealing. This is done to remove any type of internal stresses from the amorphous metal sheets so that they can optimize magnetic properties. The heat treatment process helps align the magnetic domain and improve performance of the amorphous metal.
The core manufactured using the amorphous metal alloy initially has low mechanical strength due to the grain structure of the metals and very thin sheets being used in the manufacturing. So to deliver extra mechanical strength to the core, lamination of the entire assembly is done. The lamination acts as a protective casing or coating that gives extra mechanical strength and also delivers insulation.
Silicon Steel Core Construction
During the manufacturing of silicon steel, the molten silicon steel alloy is first subjected to a rapid cooling to a cold rolling process followed by the heat treatment process called annealing to remove all types of extra stresses that are induced in the sheet during the cold rolling process. The heat treatment process and the cold rolling process produce a grain oriented structure in the silicon steel sheets that enable easy magnetizing in the material. This grain structure also helps reduce and minimize the hysteresis losses when the magnetic flux flows in the material.
Like the amorphous core material manufacturing, the silicon steel core manufacturing also involves very thin sheets of the silicon steel that are obtained in the form of long thin sheets or in coil form. The thickness of the silicon steel sheets ranges from 0.23 mm to 0.3 mm in thickness. At this thickness the silicon steel sheets offer very high permeability in the grain direction and also offer very low hysteresis as compared to non oriented silicon steel.
The sheets are then cut into the required shape and size and then stacked up to construct the transformer core. The silicon steel sheets are usually cut in common shape like E I, C or step lap configuration. Among these configurations, the step lap design is specially used to minimize joints and air gaps in the final transformer core assembly and this also reduces noises and core losses.
Like the amorphous metal sheet, the silicon steel metal sheet being such a thin sheet has very limited mechanical strength and needs support to resist the stresses induced during the transformer working. The sheets also need insulation between the sheets when they are stacked up to make the transformer core.
This is done to laminate the silicon steel sheets and the process involves coating of insulating oxide layers on each sheet of this silicon steel. This can also be achieved using varnish to electrically isolate each sheet before it is stacked up in the transformer core.
Working and Efficiency Comparison
The working principle of the transformer core remains the same irrespective of what type of material is being used for the manufacturing and what shape or configuration is adopted. However the difference lies in the overall working efficiency of the transformer core and how each specific core performs in different operating conditions.
The amorphous core exhibits significantly lower hysteresis losses and eddy current losses however the silicon steel core offers higher core losses due to its crystalline structure. On the other hand the silicon steel core has much higher saturation flux density making it more suitable for high power and high load applications.
The amorphous core transformer offers reduced no load losses and their losses are about 60 or 70% lower as compared to the silicon steel core. This makes the amorphous core transformer an ideal choice for those applications where there are extended idle periods or there is constant energization. Using the amorphous core material in the transformer will lead you to have lower energy bills due to lower losses and reduced carbon footprint contributing to environmental sustainability.
Reading on: Transformer Efficiency: The Ultimate FAQs Guide
Cost Comparison
Although the amorphous alloy transformer core offers numerous benefits and higher efficiency with reduced core losses, the cost of the transformer increases manyfold due to higher cost of the amorphous core.
The cost of the transformer also increases due to the brittle and fragile nature of the amorphous material that requires you to use very precision cutting machinery and similarly high precision assembly units for stacking and assembling the transformer core.
This makes the assembly process slower and much more complex as compared to the standard procedure. And due to these precision machining and assembly procedures, the overall process of amorphous core manufacturing is not easily adaptable in making any design modification. All of this increases the cost of the transformer core and thus increases the final cost of the transformer.
Opposite to this, the silicon steel core does not offer high efficiency and reduced losses like that of the amorphous core, however the cost of the final core and the transformer itself is much lower when compared with the amorphous core transformer.
This is because the silicon steel material is very easy to cut, stack and then assemble in the transformer core configuration. The process does not need anything specific or specially designed machining and assembling processes. This also makes silicon steel core ideal for mass production and standardization that reduces the cost of the final product.
It is due to these reasons that silicon steel cores are a very cost effective and well supported option in the industry.
Applications and Use Cases
Due to their high efficiency and reduced overall losses, the amorphous core transformers are highly recommended for all types of energy efficient applications like commercial buildings, residential buildings and digital assets related industries like data centres, AI models and crypto mining centres.
As amorphous core transformers are considered to be more environment friendly and due to their efficient working these transformers are also recommended for green energy initiatives like solar power plants and wind turbines. The amorphous core transformers are also recommended for smart cities projects and also for small and micro grids to power small industries or small residential areas.
Quite opposite to the amorphous core transformer, the silicon steel core transformers are designed and developed for mass applications in high power applications. The silicon steel core transformers are highly recommended for power transformers and power generation plants. These transformers are also recommended for large industrial applications where heavy machinery is being used and more than one transformer might be needed to power the industry. Silicon steel transformers are an important part of our electricity transmission and distribution systems and they are widely used in all types of substations.
Conclusion
The electrical transformer core is the most crucial part of the electrical transformer and plays a vital role of transferring power between the transformer windings. Amorphous core and silicon steel core are the two most widely used for the electrical transformer. Each offers benefits of its own and has certain limitations. Amorphous core transformers are considered to be more efficient and have lower core losses as compared to the silicon steel core transformer however the cost of the amorphous transformer is much more than that of the silicon steel core transformer. This is the reason the amorphous transformer is recommended for highly efficient and sensitive applications whereas silicon steel core transformer is recommended for all types of high power and mass applications.
Follow Us
Both the amorphous core transformer and the silicon steel core transformer are an important part of our electricity distribution and regulation setup. We at Daelim Transformer, offer amorphous transformers and silicon steel core transformers of all types and sizes and of different power capacity. All our electrical transformers are designed and validated as per international standards and we also deliver custom made transformers for specific clients. If you have any questions related to the electrical transformers you can contact us and our team will handle your problem at earliest.
Related Products
Related Article
Complete Introduction of Energy Efficient Transformers
his article provides a comprehensive overview of energy efficient transformers, explaining their importance, working principles, efficiency factors, and key differences from standard transformers. It also covers materials, manufacturing techniques, selection criteria, regulatory standards, and future trends such as superconducting cores and IoT integration in power distribution systems.
Comprehensive Guide on ANSI Transformer Standards
ANSI transformer standards ensure the safety, reliability, efficiency, and compatibility of electrical transformers in the U.S. They guide transformer design, materials, testing, maintenance, and installation to meet national and international requirements. These standards promote uniformity across manufacturers, ensuring stable integration into power systems. Daelim Transformer offers ANSI-compliant transformers of various types and capacities.
How to Safely Transport Power Transformers Using a lowboy Trailer
Power transformer transportation requires specialized lowboy trailers for safety and stability due to their massive size and sensitivity. Key factors include weight calculations, route planning, weather, permits, and secure loading. Daelim Transformer offers expert transformer design, customization, global delivery, and reliable after-sales support, ensuring safe and efficient transport from factory to installation site.
A Complete Guide on Transformer FAT Test
Transformer FAT (Factory Acceptance Test) ensures that transformers meet design specifications and international standards for safe, reliable, and efficient operation. It includes inspections and electrical tests like resistance, insulation, and voltage tests. Performed by the manufacturer, client, and sometimes third-party, FAT helps prevent failures, reduce maintenance costs, and ensure long-term reliability.
Should Dry Type Transformers Be Installed Indoors or Outdoors?
This article compares indoor and outdoor dry type transformer installations, covering requirements, applications, ventilation, safety, and pros and cons. Indoor setups offer better protection and security but require more space and cooling. Outdoor installations save indoor space and reduce fire risks but need weatherproofing and enhanced security. Installation choice depends on environment, safety, and application needs.