The Ultimate Guide To Core Type Transformer
Transformers come in various designs, each tailored for specific applications. Core type transformers are one of the prominent designs, known for their efficiency and mechanical stability. This guide delves into core type transformers, focusing on their construction, benefits, and comparison with other types.
What is a Core Type Transformer?
A core type transformer features a core that is surrounded by the windings. This design simplifies assembly and insulation while enhancing the transformer's efficiency. Core type transformers are favored for their mechanical stability and ease of maintenance.
Core Type vs. Shell Type Transformers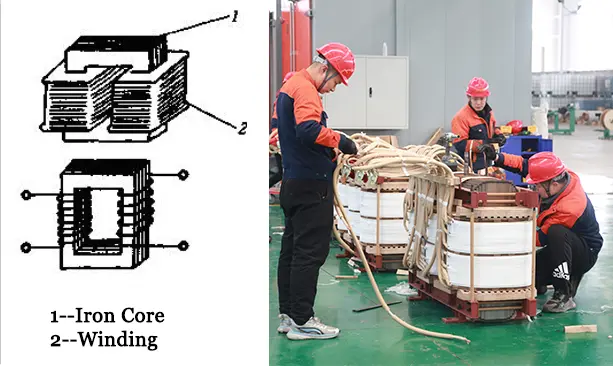
Transformers generally fall into two core construction categories: core type and shell type.
-
Core Type Transformer: The core surrounds the windings. It is advantageous for its mechanical stability and suitability for high-frequency currents. Core type transformers use iron cores made from laminated silicon steel to reduce energy losses and improve performance.
-
Shell Type Transformer: Here, the winding is surrounded by the core. This design is more compact and suitable for low voltage applications. It is easier to assemble but typically less efficient for high-frequency currents compared to core type transformers.
You may enjoy: 2500 kVA Pad Mounted Transformer
Core Materials
Transformers predominantly use silicon steel sheets for core construction. These sheets, often 0.35-0.45mm thick, are laminated to reduce energy losses. Silicon steel's high permeability allows for efficient magnetic flux conduction, enhancing transformer performance and longevity.
Construction and Types
-
Single-Phase Core Type Transformers:
- Double-Leg Structure: Features two vertical iron core columns with windings around each. This structure is compact, suitable for small and medium-sized transformers.
- Single-Leg Side-Yoke Structure: Includes a central core column with side yokes. It is used for larger single-phase transformers and offers reduced height.
-
Three-Phase Core Type Transformers:
Three-Leg Structure: Common in medium and large transformers. It has three core legs with symmetrical windings, providing balanced magnetic flux.
- Five-Leg Structure: Includes an additional central core and side yokes. It is used for large transformers requiring reduced core height for transportation.
Reading on: Let's know more about the construction of a three-phase transformer
Applications
Core type transformers are versatile, used in:
- Power transmission and distribution
- Industry and commerce
- Renewable energy and battery storage
- Data centers and oil and gas exploration
Reading more: Different Transformer Types and Their Applications
Winding Types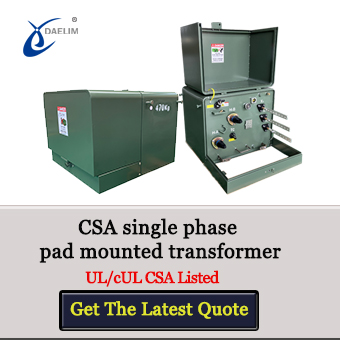
- Single-Winding Transformers: Also known as autotransformers, these have primary and secondary windings in series.
- Two-Winding Transformers: Common for distribution transformers, with separate primary and secondary windings.
- Three-Winding Transformers: Used in high-power applications to connect three different voltages.
Advantages
- Mechanical Strength: Core type transformers offer better mechanical stability and can withstand external forces.
- Reduced Losses: Laminated cores help minimize iron losses and flux leakage.
- Efficiency: Effective for high-frequency currents due to reduced eddy current losses.
- Improved Cooling: Greater surface area aids in heat dissipation, enhancing performance and lifespan.
Read more about losses: The Ultimate Guide To Losses In Transformer
Disadvantages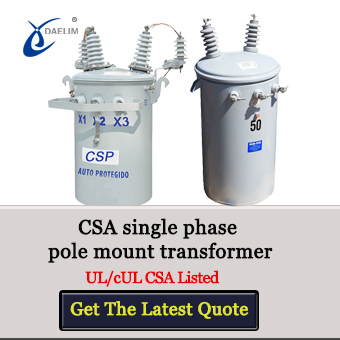
- Cost: Core type transformers are more expensive to manufacture and maintain.
- Maintenance: Regular upkeep is required, especially in extreme environments.
- Noise: They can be noisier due to cooling fans and other components.
Core Type vs. Shell Type: Which is Better?
Choosing between core type and shell type transformers depends on specific needs. Core type transformers excel in high-frequency applications and offer robust mechanical stability, whereas shell type transformers are more compact and easier to install.
Try for free: The ultimate guide to ONAN transformers
Conclusion
Understanding the distinctions and applications of core type transformers is crucial for selecting the right solution for your needs. Daelim Transformer offers expertise in core type designs, ensuring high efficiency and performance. Contact us to discuss how our transformers can meet your specific requirements.
For more information on transformer types and their applications, consult with our experts at Daelim Transformer.
Click here to check Daelim International Transformer Projects.
Related Products
Related Article
13.8 kV 10.5 MVA Substation Transformer for Ecuador
A customer from Ecuador contacted Daelim Transformer for a 10.5MVA substation transformer (13.8kV high voltage, 2.4kV low voltage). Daelim Transformer provided a customized solution, conducted virtual factory tours, ensured rigorous quality control via video inspections, and offered post-delivery online training and ongoing support, fostering a successful partnership.
20MVA Power Transformer for the United States
This project involves the development of a 20 MVA three-phase power transformer tailored for the United States market. The primary voltage is 24.94kV, and the secondary voltage is 4.16kV, indicating it functions as a step-down transformer. The design and production fully comply with IEEE C57.12.00 standards and have passed third-party UL team testing. All accessories also adhere to IEEE standards. FR3 vegetable oil serves as the insulating liquid for the transformers.
2600 kVA Pad Mounted Transformer For Crypto Mine In Kansas
This morning, I received the on-site photos of the pad-mounted transformers from the customer, and I was overwhelmed with excitement and joy. These pad-mounted transformers are installed at a 20MW crypto mining site in Kansas, USA. A total of 5 sets of 2600 kVA pad-mounted transformers, all UL-listed, are being deployed at this site. Currently, 3 sets have already been installed onsite and are scheduled to be powered on imminently.
Canadian 69 kV Substation Transformer Project
Today, we are excited to present a case study on a 69 kV substation transformer project by Daelim Transformer. Our Canadian client required a step-down transformer for their substation to connect with the hydroelectric grid in Quebec.
4500 kVA Substation Transformers for Australian Mining Site
Today, we introduce a project by Daelim Transformer aimed at supplying transformers to a mining site in Australia. This project entails the provision of two units of 4500 kVA substation transformers tailored to fit the narrow confines of mining tunnels. Due to space constraints, the transformers need to be compact in size and mounted on mobile racks for easy maneuverability within the mine shafts. This necessitates meticulous design to meet the strict dimensional requirements set by the client.
Supply of 37.5 kVA Single Phase Pad Mounted Transformers for Canadian Utility
Today, we are excited to introduce a project undertaken by Daelim Transformer aimed at supplying transformers to a Canadian utility. This project involves the delivery of 80 units of 37.5 kVA single-phase pad mounted transformers, specially designed to meet the utility's requirements. With a high voltage (HV) rating of 24940GRDY/14400 V and a low voltage (LV) rating of 240/120 V, these transformers are vital components in the utility's infrastructure.