A Complete Guide on Transformer FAT Test
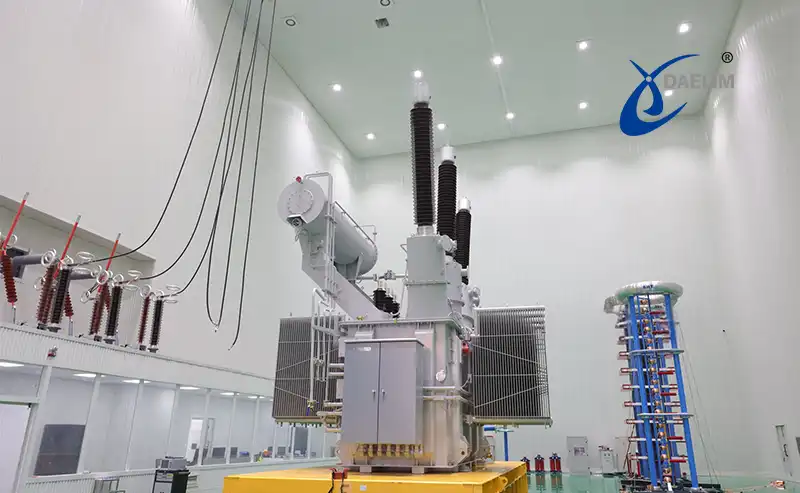
Electrical transformers are such a crucial part of our electricity distribution system that failure of an electric transformer means failure of the entire system. So to ensure that an electrical transformer has the ability to deliver the required performance in a safe, reliable and efficient manner, several quality inspecting and checking tests are performed.
These tests are widely known as transformer FAT tests aka transformer factory acceptance tests. Our article is all about understanding everything about these transformers. Our guide is for complete beginners and experts alike, delivering information that explains every aspect of the FAT transformer test.
Contact Daelim TransformerWhat is a Transformer FAT Test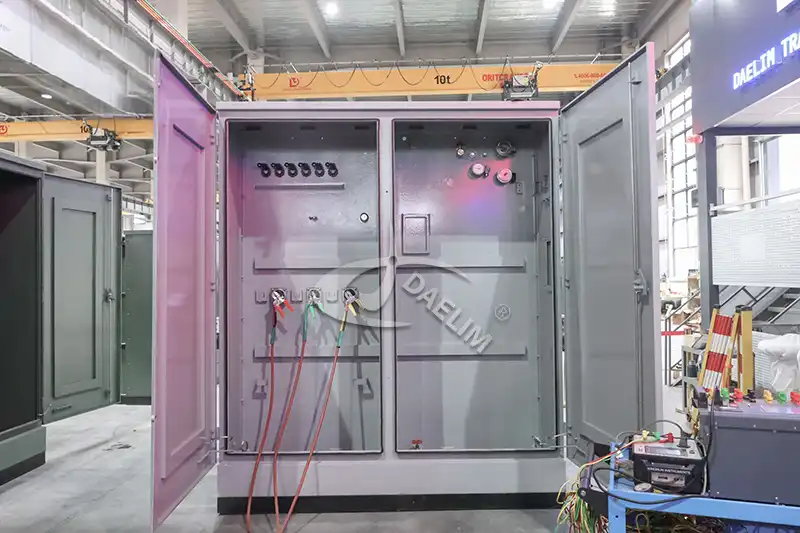
The transformer FAT test is a set of series inspections, measurements and some particular tests that are performed on an electrical transformer. These inspections, measurements and performance tests are done to verify that the transformer has been built according to specifications mentioned by the manufacturer, related international standards and requirements set by specific customer or applications.
When Transformer FAT Test is Performed
Transformer mer FAT test is performed after the successful completion of the transformer construction as per client requirements. It is done to check quality of design calculation based on which transformers were designed, detect any manufacturing defect or mistake made during the assembly process.
Who Perform Transformer FAT Test
The factory acceptance test is usually performed at the factory floor by the team of engineers including members of the quality assurance department of the manufacturer, client representative, and sometimes third party representative usually when working on large power transformers. Each member has its own duties and role in the transformer FAT process.
You may enjoy: How to test a power transformer?
Manufacturer QA/QC Team
The manufacturer quality assurance or quality control team will be responsible for performing all the tests involved in the Transformers factory acceptance test. They will be responsible for setting up the Transformer for the test, gathering all their tools and performing each and every step of the test as per standard. They will also be very responsible for generating all the results and generate a comprehensive report that includes results of each and every test performed.
Client Representative
Either an individual or a complete team from that act as a client representative or also present on the site and they are there to witness the entire process of the factory test and check the results to ensure the transparency and quality of the final transformer products. This team needs to validate the test outcomes with the requirements of the application and the specification mentioned in the procurement order.
Third Party Representative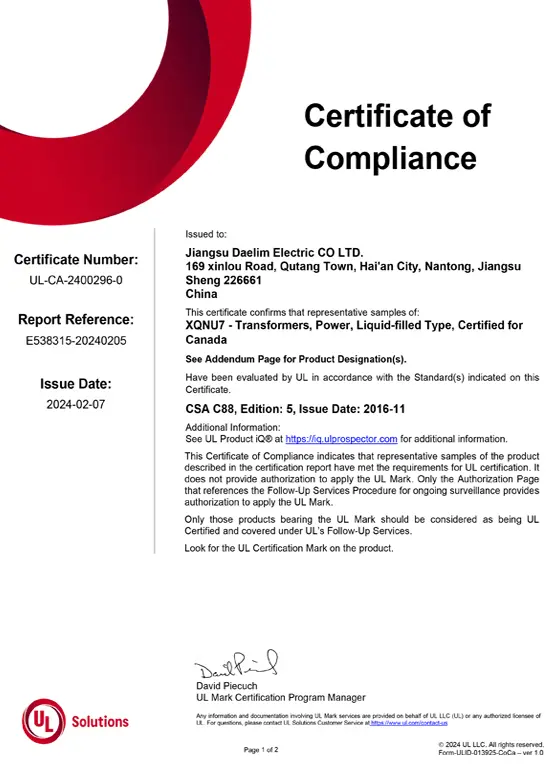
Based on the regional standards for the application requirements there might be third party representatives that work to cross check and inspect the factory acceptance test procedures and result outcomes of each test. Third party representatives are usually part of factory acceptance tests when the Transformers are being manufactured for either a very large power regulating application like national grids or they are being manufactured in high volumes.
There are three most commonly involved third party agencies that work for inspection, testing, and certification of electrical transformers.
- SGS (Société Générale de Surveillance) a globally known organization for inspection, testing and certification.
- UL (Underwriters Laboratories) works mostly in North America for safety certification.
- CSA (Canadian Standards Association) provides testing and safety services in Canada and in a number of other countries.
These globally known companies work as third party agencies during transformer FAT testing in some state of art and most modern transformer manufacturing industries like Daelim Transformer. Daelim Transformer works along with SGS, UL and CSA as their client requirements and their own standard operating procedure. Each of their transformers goes through a vigorous process of transformer testing to ensure they follow and satisfy all international standards.
Why is Transformer FAT Important?
Factory acceptance test of Electrical Transformer is a time taking and labour intensive task. There are four main reasons why performing such a time taking a labour intensive task is important.
The transformer FAT test is done to verify that the performance and all working parameters of the transformer is as per the approved drawing and Technical requirements
Transformer FAT testing is also done to confirm the adherence to the transformer manufacturing facility with all International standards like IEEE, IEC and ANSI.
These tests also help prevent on site failures; it overall reduces the cost of maintenance and repair work that might happen due to lower quality of sudden Transformer failure. It also helps reduce warranty claims and down time in any sensitive application.
Key Tests Included in Transformer FAT
There are about 11 different tests in the factory acceptance test of Electrical Transformer and in any given situation or specific requirement any set of these tests can be performed on the Electrical Transformer.
Visual and Dimensional Inspection
First test that might be performed during the transformer FAT test is the visual inspection of the Electrical Transformer to check for all the physical aspects of the transformer like body paint and location of different parts. During the factory acceptance test the visual inspection test also involves checking and verifying the overall dimensions of the Electrical Transformer as some applications might have strict space constraints against which the Transformer over all dimensions are made.
Winding Resistance Test
One of the main tests that is performed on almost each and every Electrical Transformer is the winding resistance test of the transformer winding. This test is done to ensure that there is no issue with the Transformer winding and the winding section is free from any type of open circuits short circuit or any type of poor connection.
Ratio and Polarity Test
Similar to the winding resistance test the turn ratio test and the polarity test of the transformer winding is done to ensure that the number of turns in Electrical Transformer winding is as per the design calculations and the polarity is correct as per the client requirement. The test helps confirm the correct voltage transformation and phase relationship in electrical Transformers.
Insulation Resistance Test
Different parts of electrical Transformers need to be insulated from each other and to check these the insulation resistance test is performed once the Transformers assembly. The insulation resistance test is done to ensure that the insulation resistance between the winding and the ground connection is as per requirement. This test gives the results in terms of Value of resistance in Ohm and the tool used for this test is called megohmmeter.
Dielectric/Withstand Voltage Test
Dielectric or withstand voltage test is a type of test that is done to ensure the insulation strength against high electrical voltage. During this test High Voltage is applied on the Transformer winding to ensure the insulation strength of the winding section is sufficient to resist the high voltage of the Electrical Transformer. Due to this reason this test is also called the applied voltage test.
Induced Overvoltage Test
The induced overvoltage test of the Electrical Transformer is also known as the double voltage double frequency test. In this test the Electrical Transformer is subjected to twice the electrical voltage than its operational voltage at this frequency that is twice the frequency of its normal operation. This test is done in order to test the insulation ability of the Electrical Transformer parts in case of any sudden Electrical surge.
Short Circuit Impedance and Load Loss Test
Short circuit impedance and load loss test is a test of Electrical Transformer that is done to assess the performance and reliability of the Electrical Transformer in the event of a loading condition and operating environment. short circuit in one Transformer winding while applying a voltage to the other. This helps measure impedance voltage and load losses like copper losses and core losses in Electrical Transformer.
Vector Group Verification
Group verification is done in order to ensure that the Transformer internal winding configuration is correct. This test ensures that the winding configuration of the Electrical Transformer is made as per the requirement put by the client and the system configuration is compatible with the great system for which the electrical Transformer has been manufactured.
Temperature Rise Test
Electrical Transformer produces a lot of waste heat when operated at full operation load and to test whether the Transformer cooling system is sufficient to remove that waste heat at temperature is tested. This test is performed by operating the Transformer at its maximum capacity for a given period of time and measuring the rise in temperature of the transformer winding.
Functional Checks
Electrical Transformers have several parts attached to the Transformer that help the Transformer in various operating conditions and load requirements. In order to ensure that all these attached parts work perfectly, several inspections and tests are performed on these electrical parts.
However, most of the time working of these electrical parts is tested while the transformer is being operated and tested during factory acceptance testing. Some common parts that are tested in Electrical Transformer during this test are as follow
- On load tap changer is tested when the transformer is being operated and functionality of the tab changer is checked during this test.
- There are several temperature gauges installed in Electrical Transformer and working and calibration of these temperature gauges Is done before and after being install in Electrical Transformer
- In oil type Electrical Transformer oil level is crucial for transformer efficiency and proper working for that oil level indicator is stored in an Electrical Transformer that is tested and calibrated before installation.
- Transformer cooling systems can have electrical fans and the electrical system can have relays and alarms whose functionality is checked after installation.
Optional and Specialized FAT Tests
There are several specialised tests over which you can see optional tests that can be performed during the factory acceptance testing of Electrical Transformer. These optional or specialised tests are completely dependent on the Electrical Transformer type or the application for which the transformer is being manufactured. These tests can also be a part of any specific standard that the Electrical Transformer needs to satisfy based on the regional or application standard.
Partial Discharge Test
The partial discharge test is done to elevate the insulation health of the Electrical Transformer. This test measures the insulation held by detecting the internal discharges that might happen due to insulation failure or weak insulation.
Sweep Frequency Response Analysis (SFRA)
Frequency response analysis is a dedicated test that is performed to assess the mechanical integrity of Power Transformers only, this test measures the mechanical integrity of the Electrical Transformer part by measuring the electrical transfer function over a wide range of frequencies. This test has detected any type of mechanical damage in the Transformer parts like winding deformation or core movement or any type of Broken clamping structure.
Dissolved Gas Analysis (DGA)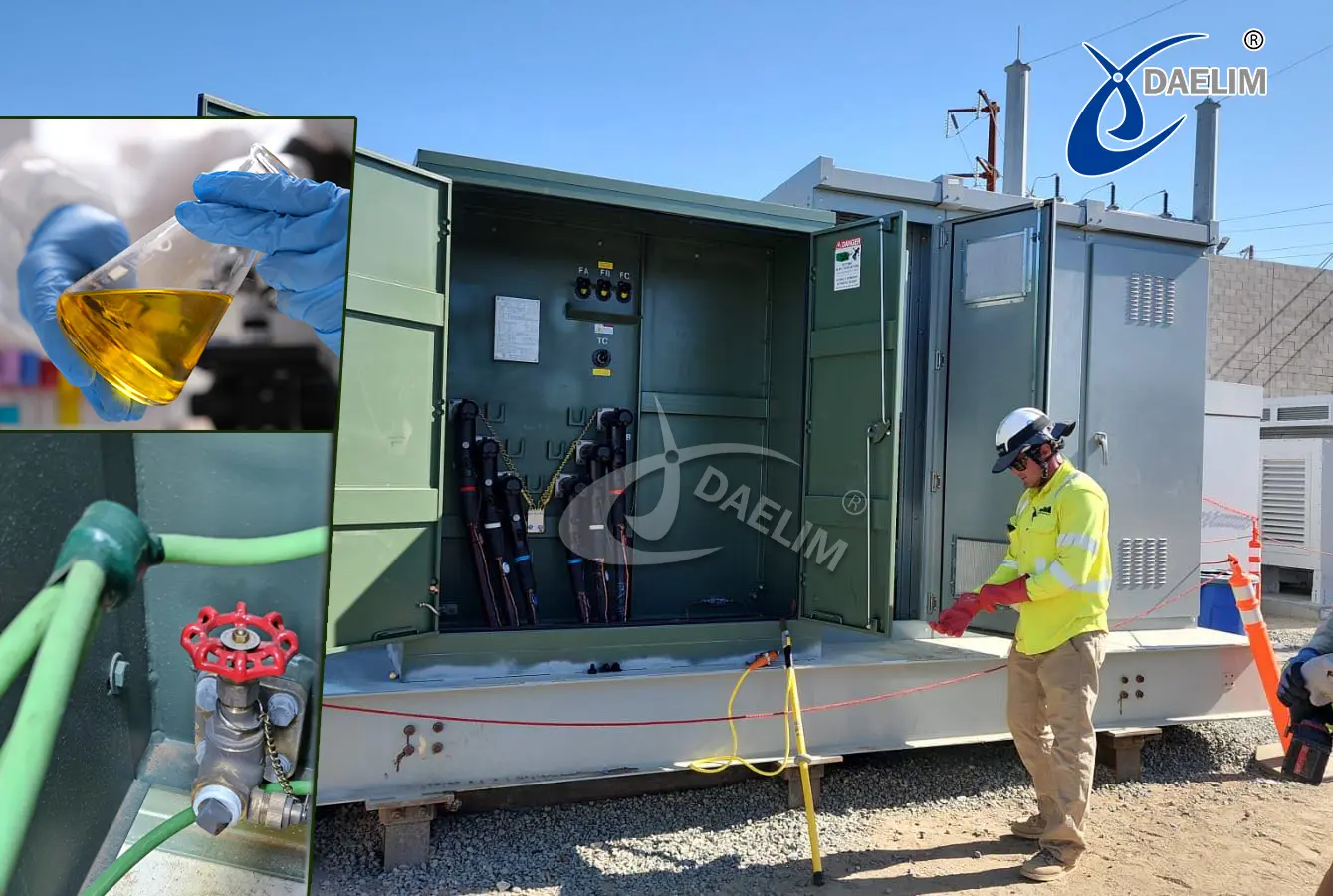
The dissolved gas analysis is done in oil type electrical Transformers only and it is done to check the quality of the oil present in the Electrical Transformer. This test is done initially to check the quality of the oil used in the Transformer before it is being used. Most of the time this test is performed during the regular maintenance or scheduled instructions to assess the Transformer oil life.
Noise Level and Vibration Measurement
Applications where noise level over vibrations are a serious concern noise level or vibration measurement test is performed to check the electrical noise and vibration generated by the Electrical Transformer when it is operated at its maximum operating load.
Transformer Factory Acceptance Test Checklist
It depends on the sequence of tests that you need to perform during the factory acceptance testing however there are some tips for you to understand or prepare yourself before you start the testing sequence or help you during Record Keeping of the test.
- You should have a proper identification of all the electrical equipment tools and machinery that will be used during the test and have a sequence of serial numbers of all the parts that or will be used in the test.
- You should have a complete package of Pre test documentation that will help you conduct tests smoothly and have a proper record of each test and validate. you all Have all the technical drawings, written technical specs and approved test plan for your transformer FAT testing.
- Usually have a complete sequence of tests that you need to perform step by step and take measurements and record the readings.
- In case of sensitive application you should have a pre approved format for Record Keeping and result making in order to avoid any ambiguity at the end.
- Before starting any test during the factory acceptance testing you should have a complete post test review and sign of section.
Standards Governing FAT Procedures
As this factory acceptance testing is such a crucial part of ensuring the reliability, safety, and high performance of Electrical Transformer red there are a number of international standards that are being issued by various standard issuing authorities for different regions of the world. We will discuss three widely used International standards for these factory acceptance testing of Electrical Transformer.
IEC 60076 series
The IEC 60076 series is a sequence of documentation that issues requirements and testing procedures for factory acceptance testing of Power Transformers only.
Learn more about IEC 60076 Standard
ANSI C57 series
The ANSI C57 is a series of standards that issue standard performing procedures of tests and the performance of Electrical Transformer during factory acceptance testing. These standards are specifically developed for the United States of America however they are also used in different parts of the world where other electrical related American products and standards are also being followed.
IEEE C57.12.90
The IEEE C57.12.90 Is a standard that issues documentation and different test codes for factory acceptance testing of liquid immersed distribution and Power Transformers.
Reading more about IEEE C57 Standard
Conclusion
Electrical transformers are equal part of our Electricity Distribution system so they always go through a very strict factory acceptance testing procedure to ensure that each and every Electrical Transformer that has been manufactured and delivered against specific requirements is capable enough to deliver safe, reliable and efficient performance. There are about 11 different types of test that can be performed on any Electrical Transformer and the combination of these tests depends on the Transformer type and application against which the transformer is being used. There are three types of teams involved during these transformer FAT testing, a quality control team of the manufacturing department, the client representative and sometimes third party representative to ensure transparency.
Follow Up
Daelim Transformer has been designing and manufacturing electrical transformers of all types and sizes for over 25 years. Each and every electrical transformer that is manufactured in our plant goes through a very strict factory acceptance testing procedure, and each product is evaluated based on a wide range of international standards, including ANSI, IEEE, and IEC. We also have extensive experience with certifications and testing requirements from organizations such as CSA, UL, and SGS, ensuring that our products meet the highest levels of global compliance and quality.
If you have any questions related to Electrical Transformer then you can contact us and our team will help you to resolve your problem at earliest.
Related Products
Related Article
Comprehensive Guide on ANSI Transformer Standards
ANSI transformer standards ensure the safety, reliability, efficiency, and compatibility of electrical transformers in the U.S. They guide transformer design, materials, testing, maintenance, and installation to meet national and international requirements. These standards promote uniformity across manufacturers, ensuring stable integration into power systems. Daelim Transformer offers ANSI-compliant transformers of various types and capacities.
Canada 69kV Power Transformer Testing
After a meticulous 16-week production process, we are pleased to commence the factory testing phase for the transformer. At Daelim Transformers, we adhere to the highest industry standards, conducting comprehensive tests to ensure the utmost quality and performance of our products. Each project undergoes rigorous testing in accordance with the relevant standards set by IEEE and CSA.
Understand the Transformer Lifespan
Electrical transformers have a critical role in power distribution and a defined lifespan known as "useful life." Sudden failures disrupt electricity supply, making timely replacement essential. Key factors affecting lifespan include usage, maintenance, and environment. Understanding these helps predict remaining life and extend transformer longevity through proper care and condition monitoring.
How to Safely Transport Power Transformers Using a lowboy Trailer
Power transformer transportation requires specialized lowboy trailers for safety and stability due to their massive size and sensitivity. Key factors include weight calculations, route planning, weather, permits, and secure loading. Daelim Transformer offers expert transformer design, customization, global delivery, and reliable after-sales support, ensuring safe and efficient transport from factory to installation site.
Complete Introduction of Energy Efficient Transformers
his article provides a comprehensive overview of energy efficient transformers, explaining their importance, working principles, efficiency factors, and key differences from standard transformers. It also covers materials, manufacturing techniques, selection criteria, regulatory standards, and future trends such as superconducting cores and IoT integration in power distribution systems.
How to test a power transformer?
Power transformers need to undergo rigorous testing before they leave the factory and are installed to ensure that the transformers can operate safely and efficiently.